The opportunity to undertake research into metal 3D printing and 3D printed resin sand moulds to explore new bell designs printed in a variety of metals at CSIRO’s Lab 22 Materials technology is just wonderful.
I need to outline a brief history to bell tuning to make the research I am undertaking at Lab 22 sensible.
Since an interest developed in Europe’s Middle Ages to refine the musicality of bells (from adding bells to bell towers and so generating musical pitch intervals between these grouped bells), there has been an ongoing quest by campanologists to exert control over the partial frequency ratios that together make up the sound of a bell and constitute the clarity of pitch this sound generates.
A bell is in tune in two separate ways. The pitch of a bell is given by its scale, such that a bell exactly scaled to half its size will sound exactly an octave higher and a bell scaled twice its size will sound an octave lower. The particular pitch of a bell within an octave is therefore a mathematical ratio of the bell’s size between the scale doubling or halving, regardless of intonation (such as equal temper, just tuning or any other musical scale chosen for the octave).
The more difficult tuning of a bell is to find a bell profile (its inside and outside shape) that puts the lowest seven or less partial frequencies that the bell generates into a harmonic array. When a profile is found that achieves this, the dominant partial frequencies generated in the bell support the lowest (called the fundamental) frequency, giving the bell’s ring a distinct clarity of pitch to the ear of the listener. The human ear seeks harmonic sounds in the world and has great subtlety in finding them as the human voice, a column of vibrating air, naturally produces harmonic overtones (partial frequencies). Most musical instruments use the natural harmonics of vibrating strings or vibrating air columns to generate harmonic pitch with great clarity.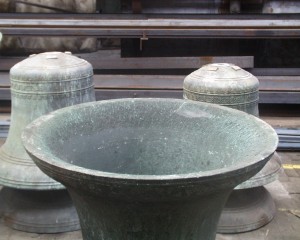
The quest to harmonically tune the bell started with bell founders chiselling their cast bell, sometimes finely, but often quite crudely in an attempt to better control the frequency array of the bell. The chipping and filing are attempts to change the shape of the bell’s profile to shift partial frequency ratios and so improve the clarity of its pitch when rung. The inventive step to use a lathe to scrape metal from the surface of the bell, usually internally where it doesn’t show, to tune the partial frequencies and put them in as best a harmonic array as possible was made (and subsequently) forgotten in the Netherlands of the 1600s and again in Europe around 1900. Apart from the ‘Foreign note’ of a minor third partial frequency locked into the European bell due to its profile, the bell founders managed by foundry iteration to tune the European bell to a harmonic sequence of partial frequencies.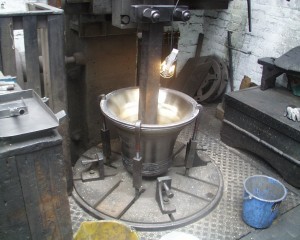
In the middle 1980s Dr Lehr at Royal Eijbouts Bell Foundry collaborated with Eindhoven University of Technology to use Finite Element Analysis vibrational engineering software to develop a series of new bell designs. They attempted a fully harmonic bell to finally remove the minor third ‘foreign note’ partial frequency, with their virtual model starting at a traditional European bell profile. The computer result, a unique solution, was carefully cast as an actual bell, but only to discover the bell started at one pitch and finished at another.
Commissioned to undertake the Melbourne International Festival’s Federation Bell Projects in 1998 Australian Bell collaborated with RMIT University’s Aeronautical Engineering Professor Tomas whose Finite Element Analysis software ReShape was used to optimise a number of new musical bells including a fully harmonic bell, found using a cone profile as the virtual model.
In 2014 Australian Bell was commissioned by the LongNow Foundation to invent, cast and tune 10 ‘Difference-Tone’ bells for the 10,000-year Clock project being constructed to be installed inside a mountain in Texas, and designed to operate, and ring, for the next 10,000 years. Collaborating with ADVEA Engineering using ReShape software a bell profile was optimised that, when cast using 3D plastic prints as foundry patterns, did not ring a difference tone, but made its discovery possible with a careful and very slow manual tuning process of a cast bronze bell taken from the 3D print pattern. A ‘difference-tone’ is generated when a fundamental partial frequency is sounded with its perfect fifth partial frequency. The resulting pitch has the psycho-acoustical effect in the ear of the listener to generate a pitch that is an octave below the fundamental (lowest) frequency of the sounding instrument. This bell design allowed a bell four times smaller than ordinarily needed to sound the very low pitch of C 65 Hertz, which was perfect for the confined spaces inside the clock, inside the mountain. 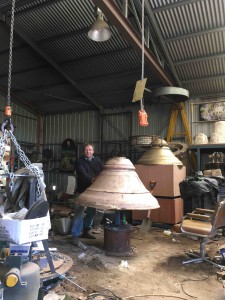
These bells are digitally designed with great accuracy and to transfer the virtual information unmolested into an actual cast bell required the accuracy of 3D printing of foundry patterns and the use of resin sand moulds.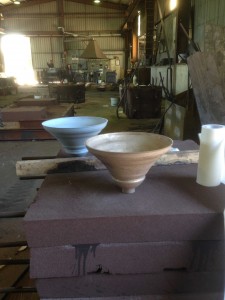
My research at Lab 22 is to explore bell designs, particularly the Australian invention of the ‘Difference-Tone’ Bell design, as direct metal 3D prints. The vagaries of sand moulding and hot metal casting can be eliminated through this process and bells can be manufactured at the highest levels of accuracy. After all, the distinguishing feature of casting bells throughout history compared to regular foundry work has always been the high levels of accuracy required to preserve the exacting musical demand being made on bells. Early on this kept bell foundry work hidden in the monasteries, and later, in the secretive world of the few specialist bell foundries making musical bells.
Danny Hillis, the founder of the 10,000-year clock project, has given his blessing to this research to print the world’s first ‘Difference-Tone’ Bell and like him, I cannot wait to hear the printed bell ring.
It is a great privilege to work with Dr Daniel East and other researchers at Lab 22 on this project. Dr Anton Hasell Australian Bell.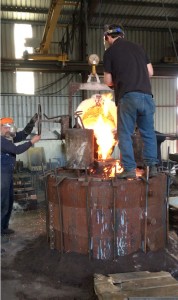